项目背景
随着人们对产品功能需求的不断提高,产品设计中所需要涉及到的各个学科只是的深度与广度也在不断发展。各个学科内部呈现不断细分的趋势,而学科间的耦合关系也变得越来越复杂。这一发展趋势在飞行器总体设计上尤为显著。
另一方面,随着物理样机成本的不断攀升、虚拟样机成本的不断下降,虚拟产品开发被制造业大量采用,设计过程对仿真的依赖程度越来越高,仿真分析的复杂程度和数量不断提高,飞行器设计中仿真分析工程师的人数也急剧增加。因此,产品的仿真分析往往需要结合大量不同的仿真分析工具以及用户自己编写的专业仿真程序。这为仿真分析工程师带来了巨大的工作量。
需求分析
为了减少仿真分析工程师不必要的工作量,应当尽量减少重复工作,并提高仿真过程的自动化程度。
在快速设计过程中存在两大问题:一是设计对经验依赖性很高的问题;二是难以保证设计的质量。
在导弹快速方案设计中,首先,需要确定导弹的用途,并根据用途确定导弹的威力和射程等重要性能指标。然后,根据导弹的威力和射程确定导弹结构的详细尺寸。而这个确定过程需要依赖于设计师的经验。
技术难点1:如何将设计经验固化到设计平台中?
技术难点2:如何根据导弹的用途来确定导弹结构的详细尺寸?
技术难点3:仿真平台如何在仿真数据中获取设计经验?
一般来讲,在足够的设计经验基础上,我们只能保证设计能够满足需求,但却无法保证没有更好的设计。首先,传统设计与仿真的关系只有正向的根据设计来计算其性能,而无法反向由仿真结果来确定设计;其次,无法保证由仿真结果向设计的逆向求解过程的适定性。
技术难点4:如何用仿真结果驱动设计,在设计空间中寻找最优设计
导弹仿真分析涉及战斗部、发动机、气动、结构、控制、弹道等多个学科的耦合分析。学科间耦合关系紧密,而分析过程需要由多个不同的仿真工具协同计算才能完成。
技术难点5:平台搭建的团队必须具备仿真所需的所有学科的分析能力,而每个学科往往涉及多个仿真工具,建模工具、前后处理工具、解算器等,对团队技术能力有很高的要求。
为了实现快速方案设计,平台上的各个仿真过程需要实现全自动调用。计算机上的一个标准仿真过程包括内存中的输入输出数据,外存中的输入输出文件以及仿真工具。仿真平台必须具备调度仿真工具的接口,并能够自动解析输入输出文件。
技术难点6:平台必须能够调用所有仿真工具
为了完成仿真模型的自动建模,往往需要一组数据来控制设计模型,而这组数据是由仿真平台控制,并储存在内存中的。目前一般采用设计参数来控制设计模型。
多学科分析涉及多种偏微分方程解算器(结构分析、气动分析等),这些解算器在计算之前往往需要先进行几何建模、网格划分以及定义定解条件等过程。
其中网格划分的种类和质量决定着仿真分析的精度。在相同的网格数下,结构网格比非结构网格精度更高,但是,结构网格自动生成技术尚不成熟。
技术难点7:如何在保证计算精度的同时,实现网格的自动划分?
实际仿真工作中外存中的输入输出文件、脚本文件,内存中的数据,仿真工具间存在复杂的关联关系。
技术难点8:仿真工具调用难以管理
仿真分析过程往往存在巨大的计算量,其中偏微分方程解算器计算量比较大。以cfd(计算流体动力学)为例,cfd仿真的周期可达几个小时、几天甚至几周。
对于设计问题,为了探索设计空间,尝试不同的设计,往往需要分析成百上千种不同的设计,总设计数量随设计变量个数的增长呈几何级数暴增。而每个设计都需要完成一个完整的仿真分析过程,这也就成百上千倍地增加了仿真的总结算量。这样一组设计的仿真总cpu时间可能达到几年,不具有可行性。
技术难点9:如何在短时间内完成快速方案设计庞大的计算量?
技术难点10:导弹的总体设计是一个复杂的系统工程,即使是方案设计阶段也涉及上百个数据的传递问题,如何管理海量的数据?
凯发娱乐登录的解决方案
导弹快速方案设计平台解决上述问题。
首先,要进行参数化建模,可以采用catia、ug或pro ed等三维建模工具。
平台中的导弹模型有大量的尺寸数据,而实际上用来控制这些尺寸的数据仅有几个设计变量,其它的尺寸由关于这几个设计变量的函数来确定[技术难点2]。导弹其它详细尺寸数据采用工具中的函数来计算。
参数化模型能够将设计经验固化到设计平台中[技术难点1]。
其次,要将设计经验固化到仿真分析中。
对于战斗部和发动机,涉及较深专业知识,通用仿真工具难以满足仿真分析所需的效率和精度,因此选择根据被分析对象的设计编写专业仿真程序来计算。弹头专家和发动机专家根据设计经验编写战斗部和发动机计算程序[技术难点1],然后根据导弹的威力和射程来确定战斗部和发动机的尺寸,并传递给详细结构设计模型[技术难点2]。
导弹仿真分析中涉及到一些计算量比较大的偏微分方程求解,如有限元分析、气动分析、热分析等。以气动分析为例,气动分析对网格有较高的要求。一般先采用专业网格生成工具完成网格划分,然后采用cfd求解器进行流场仿真分析。由于导弹扰流求解域形状复杂,一般采用了非结构网格自动生成技术,为了保证精度,要对关键区域进行合理的加密,以弥补非结构网格在计算精度上的不足[技术难点7]。
搭建多学科仿真平台一般需要各个学科仿真工程师协同完成,为了实现各个仿真过程的自动化,可以录制各自学科的仿真工具的脚本以实现自动化运行并降低仿真分析对工具使用的技术门槛[技术难点5]。
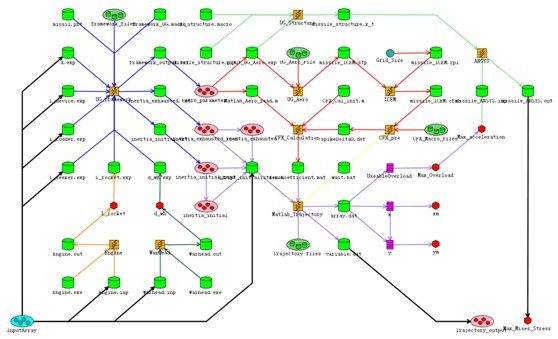
仿真工具集成平台可以采用optimus、isight或slm等软件。
以optimus为例,可以采用通用接口实现仿真工具的调度[技术难点6]。optimus自带实现试验设计、响应面建模、优化设计以及鲁棒性与可靠性设计等功能。其中试验设计、响应面建模等数据挖掘功能能够帮助用户探索设计空间,为用户总结设计经验[技术难点3];优化设计及鲁棒性与可靠性设计等功能可以自动寻找设计空间中的最优解[技术难点4]。
海量的数据首先要跟文件相关联,并在文件解析模块中定义输入输出规则,文件再与各个仿真工具根据输入输出关系相关联,这样数据、文件以及仿真工具的上下文关系就构成了一张紧密耦合的关系网,成为一个有组织的架构[技术难点8][技术难点10]。在此基础之上,数据往往需要保存在数据库中,便于管理[技术难点10]。
为了提高仿真分析精度,偏微分方程的求解往往引入巨大的计算量。另外,设计过程中大量的样本采集将仿真过程的计算量放大了成百上千倍,总计算量用单一cpu可能需要几年才能完成。纵观当今cpu的发展,其主频已达到上限,提高计算能力的主要手段已经变成增加cpu核数实现并行并行。为了缩短设计周期,采用并行方法是当前的趋势[技术难点9]。奥迪曾经利用optimus的并行功能将四年才能完成的仿真过程缩短到一周之内,为了实现这一过程,他们用上了800多个cpu并行计算。并行对仿真工作流的要求较为苛刻,需要资深仿真流程管理工程师才能实现。